|
 |
 |
 |
    |
 |
You can reach us by
e-mail, phone or regular
mail. We look forward
to hearing from you. 818-402-0711 more
|
|
 |
|
|
|
|
|
|
 |
 |
 |
   |
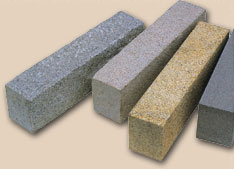 The four major processes to building a strong and functional porphyry pavers and pavement structure are:
1. FOUNDATION

2. SETTING BED

3. COMPACTING

4. GROUTING

|
A. FOUNDATION
The foundation is the firm strata that bears the load of the entire pavement system which comprises the setting bed, porphyry pavers and grout material.
A foundation must be unmoved because it is required to maintain its physical and mechanical characteristics and must be non-compressible. In the case of outdoor porphyry walkways and driveways, it must provide for the drainage of surface water by building the structure with a slightly sloped form.
Two main types of foundation exist: ballast and the concrete slab. The selection of foundation type is determined by the existing terrain and of the load to be borne by the pavement.
Ballast is a layer of compacted gravel at least 30 cm thick, consisting of chunks of larger size in contact with the ground and smaller grain above to obtain effective surface compactness.
Concrete slab instead consists of a 10 to 15 cm thick layer of concrete mixed at 250 kg of cement per m3 of suitably graded insert material, slightly reinforced against shrinkage.
B. SETTING BED
This is the actual paving bed that will be sitting directly above the foundation. It can vary according to whether the pavement is indoor or outdoor.
Outdoor: The best bedding system in terms of quality consists of crushed stone gravel (split type) 3-5 mm, polyhedral in shape, washed and sorted. This type of sand not only provides the pavement with great stability after compacting, but also drains water both during and after pavement setting. Alternatively , another kind of bedding consists of 0-6 mm cleaned and soil-free coarse sand. The sand used for the bedding layer can be mixed with dry cement added in the ratio of 150 kg per m3 of sand in order to prevent sinking. When setting binders and cubes, a bedding of sand and cement is recommended.
Indoor: The bedding layer should consist of dry-mixed sand and cement in the ratio of 400 kg of cement per cubic meter of sand. Considering that the thickness of the sand bed will decrease by about 2 cm because of installation operations, its initial thickness should range from 6 to 8 cm according to the height of the building element. During the design phase, it will always be necessary to remember that the finished pavement will consist of the thickness of the product plus 4-5 cm of pressed sand.
C. COMPACTING
Once setting of porphyry paver units and stones is completed, special large brushes are used to clean the surface. The spaces between elements are then filled with sand or a mixture of sand and cement. At this point, compacting is performed to press every single piece into final position in the bedding layer and therefore obtain a perfectly even surface. The pavement should receive at least two compacting treatments in two directions.
When sand alone is used for setting, the surface is drenched with water following the first round of compacting and before starting the second one. When sand and cement is used, the quantity of water used is less prior to the second compacting phase. After compacting, the pavement is carefully rinsed in order to remove any surplus cement.
D. GROUTING
The last phase is joint grouting between the porphyry paver units. If possible, this is done with a binding material. Among the various sealing systems the most commonly used are sand and cement slurry.
1) Grouting using sand is done by distributing over the paving, after compacting, a layer of fine sand, 0-4 mm, by filling in all of the joints using a large brush. The sand must be left on the paving for at least 15 days so as to ensure complete packing of the joints, after which the surplus sand can be removed. This technique allows for the complete recovery of the stone in the case of paving removal for excavation works, but requires greater maintenance because sand is easily removed by streaming surface water.
2) In the case of joint sealing using cement slurry, first of all it is necessary to verify that, during compacting, the depth of the joints between one element and the next has increased by 1.5-2 cm. Then the slurry, obtained by mixing equal parts of fine sand (0-4 mm), water and cement, is applied and pushed into every joint using rubber squeegees. As soon as the mortar starts to set, the surface is cleaned by removing excess mortar with large brushes aided by a flow of water.
To prevent cement from depositing on the surface of the porphyry, it is possible to apply a non-stick product using special rollers, so that the cement will remain only in the joints. Any remaining cement residue can be removed by covering the surface with wet sawdust that is then collected and removed. Any cement haloes can be removed using sulphuric acid mixed with water or other acid products commonly found on the market.
|
|
 |
|
|
 |